Facts About Flexography Printing You Should Know
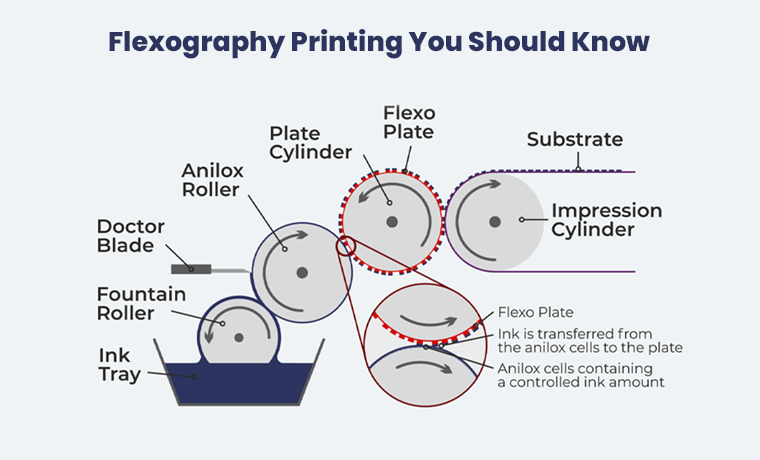
In the printing industry, as a way of creating packaging for your next project, you might have come across the word “flexography”. Whether you completely understand this printing technique or not, you will take a keen interest in learning and exploring what exactly it means and how it plays an essential role in packaging.
In this blog, you will learn about this flexography printing press, which can print large quantities of plastic, paper, metals, films, and cellophane. Let’s begin.
What is Flexography Printing
Flexography printing referred to as “flexo” is an efficient and high-speed printing method that uses flexible photopolymer plates and faster-drying inks to print on a wide range of substrates including:
- Paper
- Plastic
- Cardboard
- Metals
- Labels
- Films
- Cellophane
This printing type is ideal for large-volume production runs and can produce high-quality image resolutions with vivid colors.
Flexography Printing Examples In Top Markets and Industries
Here is the list of industries and markets using flexographic printing presses to meet their needs.
- Medical and pharmaceutical industry
- Food and Beverage industry for candy wrappers, cereal boxes, and packaging for various food products
- School and office supplies
- Boxes for product displays and point-of-purchase marketing materials
- Retail industry from shopping bags and gift bags to other retail packaging materials
- Labels such as address labels and barcode labels
- Non-woven fabrics for diapers, wipes, and other non-woven products
Flexography Vs Offset Printing: Which is Better
Here is the comparison between flexography and offset printing to highlight key differences.
Features | Flexography Printing | Offset Printing |
Printing Process | Uses flexible relief plates | Uses flat plates and rubber blankets |
Ink Type | Fast drying with low viscosity inks | High-quality inks |
Substrates | A wide range of substrates, such as paper, plastic, and metal | Primarily used for paper and cardboard |
Image Quality | Good | High-quality and offers consistent reproduction |
Print Speed | Faster and suitable for long runs | Slower but efficient for mid to long runs |
Setup Time | Quick setup and turnaround | Longer setup and turnaround |
Cost | Cost-efficient for longer runs | Economical for longer runs |
Best For | Packaging, labels, newspapers | Books, magazines, brochures |
Color Matching | It can be challenging as it requires adjustments | Excellent color consistency and accuracy |
Key Advantages And Disadvantages Of Flexography Printing
Advantages of Flexographic Printing
- Versatility: It can print a variety of substrates from plastic and brown papers to corrugated boards and acetate films, and can print high-quality patterns. It applies water-based inks, such as UV curable inks, utilizing a wide range of inks. These inks dry faster and are time-saving.
- Highly Flexible Printing Method: This method can handle millions of impressions at a time and can accommodate a wide range of cylinder repeat lengths to meet customer needs.
- Cost-Efficient: It is less expensive as compared to other printing techniques that require plates.
- Consistent Ink Transfer: Its high-speed process and flexographic inks result in consistent and faster production with limited ink use.
Disadvantages of Flexographic Printing
- Printing: It is not capable of producing meticulous artwork like offset printing produces.
- Expensive Equipment and Materials: The printing plates are costly, as these plates are bought in different colors.
- Unfit for short runs: Flexography printing is not suitable for small quantities.
How The Flexography Printing Process Works
The process of the flexography printing method begins when a photopolymer plate in a flexographic printing machine is attached to synchronously rotating impression cylinders.
Ink is transferred onto this flexible printing plate by an anilox roller intricately engraved with many smaller cells designed to retain and transfer the right amount of ink.
The printing substrate is fed into the process through an impression cylinder, another cylinder to exerts pressure for constant contact between the flexographic plate and the substrate plate.
Materials and Ink Used in Flexography Printing
This flexographic technique is applied to a variety of materials. The links can be different based on the printing media.
Paper and cardboard are used in this printing technique to produce a wide range of paper packaging products, from shipping labels to cardboard packaging.
It also depends upon the ink quality if it is good at absorption. Printing on plastic is effective as it requires inks and plates to bring the most effective outcome.
Steps To Follow In The Flexographic Printing Process
The printing process of flexographic printing is in three main phases: prepress, inking, printing, and post-press.
1. Pre-Press: This first process involves designing the artwork through design software and preparing the flexographic printing. As soon as the design is ready, the ink is transferred to the plates through a direct digital system. The plates are cut, mounted, and aligned on other plate cylinders.
2. Inking and Printing: The ink is transferred to the anilox rollers through a blade used on the rollers to remove excessive inks. Then, anilox rollers transfer the ink onto the flexo plates. After this, the plates transfer the ink to the substrates.
3. Post-Press: The final finishing and improved quality control technique is applied to produce the product. The printed substrates are dried in a while. Then they are cut, folded, and laminated as per the requirements.
Check the finished product. Make sure it is defectless during packing, shipping, and storage.
Conclusion
You will have enough understanding about flexography printing through this guide. This efficient printing method utilizes flexible flexographic printing plates to produce high-quality images on various substances.
The best thing about this printing is its ability to print different types of materials, including packaging and labels, ensuring color and sharp details to enhance product appeal, which makes it ideal in various industries.
We have explored flexo printing's pros and cons with its applications and machines to help you understand its process from pre-press to post-press.
Talk to printing specialists ready to assist you from the platform of Custom Product Packaging in regards to choosing the modern printing technique for your next project. Don’t hesitate to email us at orders@customproductpackaging.com.
FAQs
1. What is an example of flexo printing?
Food packaging is an example of using flexo printing.
2. What is the flexographic printing process popular for?
It is suitable for printing labels, cartons, and flexible packaging.
3. What is the application of flexography printing?
Widely used for packaging materials like newspapers, corrugated boxes, and envelopes.